PFB Pump Stop Versus PFS Soft Stop Features
Question:
What is the difference between the PFB Pump Stop option and the PFS Soft Stop feature?
Answer:
The difference between the PFS Soft Stop and PFB Pump Stop is that PFS Soft Stop keeps reducing the voltage to the motor until it stalls out, whereas PFB Pump Stop senses that the motor is stalling, and increases the voltage (and therefore current) to maintain speed and control the deceleration.
- The PFB Pump Control option is intended to provide controlled acceleration and deceleration of centrifugal pumps. It doesn't directly control motor current being drawn, other than what is required to control acceleration. The motor may have full voltage applied for portions of the acceleration and deceleration periods, meaning current levels close to those seen in a full voltage start can be drawn from the line, during start and stop cycles. During stopping, the pump control option keeps the motor near it's "stall point" to allow for maximum torque output and controlled deceleration of the pump.
- The PFS Soft Stop option accelerates the load with a linear ramping (increase) of the voltage applied to the connected load. It is an open loop control with simple ramp up and ramp down of the applied voltage. During a Soft Stop, the motor voltage is slowly reduced. The Soft Stop control module is primarily used on friction type applications that require an extended coast to reset stopping time. As the motor slip increases, the motor draws more current. The motor will draw up to locked rotor current times the percent of full voltage being applied at the time. For example, if a motor draws 400% of full load current(FLA) at 50% speed, and is operating at that speed when the voltage ramp is at 80% of full voltage, the motor will draw 400 X .8 = 320% of full load current (if the power system allows it). The motor sounds like it's straining during the-stop because it is.
Pump Control is usually not suitable for 'soft' power systems, because it does not limit line current. The advantage with using Pump Control option is that sudden changes in torque are prevented. The Pump Control module can also be programmed to start in a current limit mode which accelerates the motor based on a percentage of FLA (50 to 600 percent). To do the-stopping of the pump, we do not use methods where current is applied to the motor to stop the pump (ie. a selectable value based on FLA). To stop other types of loads (high inertia), we do utilize Smart Motor Braking option where the strength of the braking current is adjustable from 50 to 400% of FLA. We do not recommend using the Smart Motor Braking option to control pumps.
For additional information please contact your nearest authorized distributor, sales representative, or call our customer service or technical support lines.
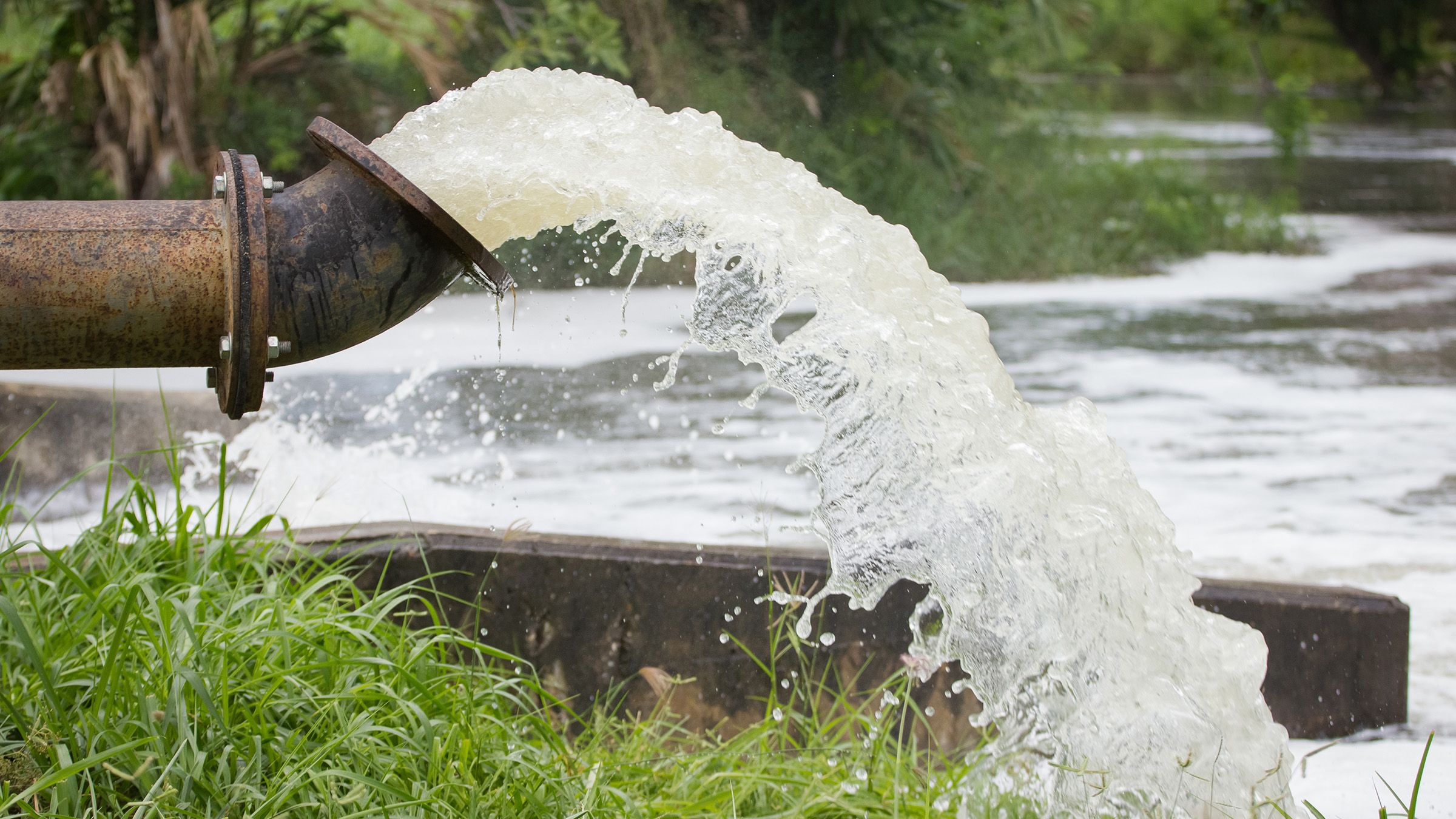